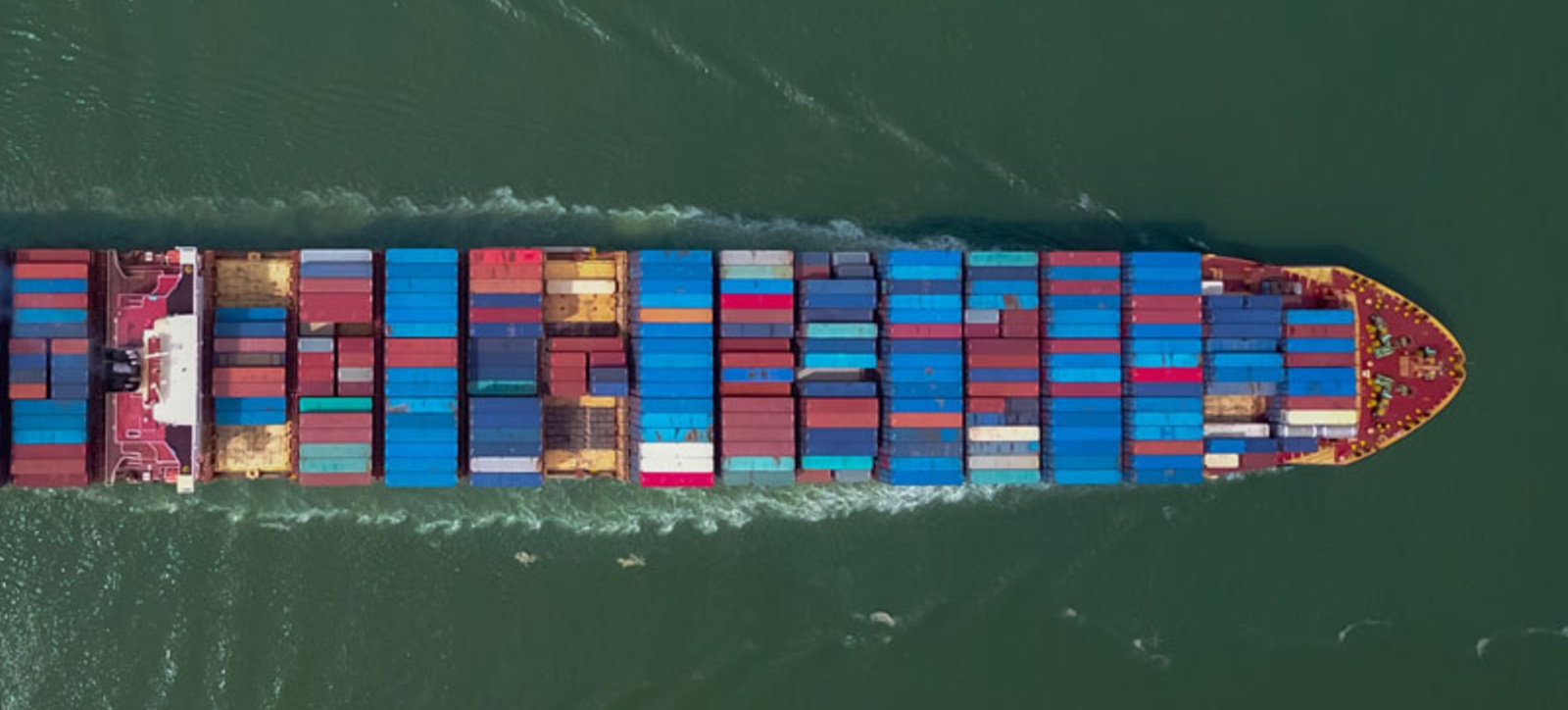
Empty shelves in supermarkets are now a familiar sight for shoppers across the Western world as the once almost invisible global supply chain has become headline news.
The pandemic has sparked a supply chain crisis that has seen a shortage of a wide variety of goods; from cars and Playstations, to Ikea furniture and Greggs sausage rolls, as just-in-time logistics have turned into an always-running-late logjam.
The sight of more than 100 ships full of containers outside Long Beach port in the US revealed the complete quagmire the once smooth-running miracle of globalisation has become. Indeed, supply chain experts are warning it will be 2023 before it is back up to speed – if it ever does with a worldwide shortage of sailors and truck drivers now apparent.
It means companies will need to be a lot more strategic about their supply chain. No longer can it be guaranteed that suppliers will be able to ship all the materials a company needs from cheaper developing countries.
Supply chain managers will need to be part of the conversation at a strategic level. They need to be part of the discussion on what goes into the product and the packaging, such as blown film plastic in personal protective equipment (PPE). UK-based firms need to be aware that all blown film is made offshore. Thus, the supply for something as simple and everyday as blown film could be problematic and so hold up a company’s own supply of products.
These decisions need to be looked at as part of a company’s strategy, because there is also a supply chain’s impact on the environment to consider, plus the company’s agility, resilience and security.
To be more strategic about supply chains companies need to ask themselves five central questions:
1 What do we compete on?
This is a vital first question. If a company is using its reputation in sustainability to attract customers, for example, this has to filter through the whole supply chain.
For instance, New Zealand lamb has a lower environmental impact than Welsh hill lamb, so even though it might be costlier importing from New Zealand it might be the way to go to remain environmentally-friendly.
This strategic decision impacts the rest of the questions to follow, because this is where a company’s core competencies lie. This is what the business needs to beat the competition and so it has to build its processes and structures around it, with the supply chain aligning to this strategy.
Sustainability is now an issue for every company, so if a firm is building a complex product, then it needs to take into account maintenance and the end of its life. Xerox, for example, decided to produce high-end photocopiers that utilise a metal frame, which is expensive, but will last forever and can be reused and sent back out in new photocopiers.
But then there are questions about how are the photocopiers collected at the end of their life? What other parts are needed to upgrade it and how that affects the supply chain?
2 What are the risks?
Next, companies need to look at the risks in the supply chain. This is not just about interruptions due to events like strikes and the pandemic, but also about losing intellectual property.
There is a long list of suppliers becoming manufacturers because they have managed to copy the very things they were paid to transport. For example, South Korean conglomerate LG didn’t exist 20 years ago; it was a sub-contractor to branded electronic suppliers. But outsourcing products or services with knowhow in them is dangerous. Firms can quickly learn how to make it, design it and then how to brand and sell it.
This is what LG did. It learned how to make a mobile phone, TV, fridge and is now a giant consumer electronics brand, among other things. Another example is Taiwanese electronics group HTC; it used to be a supplier of phones and now it makes them. Intellectual property protection can be written into contracts, but what happens when they run out? And will the contract even stop the supplier?
Companies also need to be aware of the countries and waters its supply routes travel through. Piracy has been a problem in recent years and there are some shipping lanes that are more vulnerable to this through a lack of security. Also how unionised are workers? The stronger the union the more likely it is that dock workers or road hauliers will go on strike.
Are there political risks, like Brexit, that will bring about a shortage workers? And how reliant is your company on one supplier? Car manufacturers have been caught out by the worldwide shortage of chips, for instance, where a surge in demand has left them struggling to fill the gap.
Related course: Postgraduate Award in Service Operations Management
3 Do/buy?
Following the strategic and risk questions, companies then need to decide if they build it themselves on site or buy it in from another firm?
There are other options as well; companies can source from more than one place, or they could make some of it and import the rest. The answer to these questions generally revolves around fit. What are the core competencies of your firm? For example, Apple doesn’t have any manufacturing capability, its core competency is design and it outsources the manufacturing of its iPhones and other products.
Tesla, meanwhile, has core competencies around making batteries and manufacturing an electric drivetrain. But the complexity around such competencies mean Nissan is outsourcing the battery manufacturing for its new Leaf before assembling the car at its Sunderland site.
4 Location?
Once a firm has decided to outsource some of its manufacturing or supply of material then it has to decide where they come from.
This again is down to fit. When Nissan built its assembly plant in the UK in the early 1980s, it was to serve the European market as the country was still part of the EU, so it needed to be close to a port, with a supply of skilled labour that was out of work. It also didn’t want heavy unionisation.
It came down to between Washington in the North East and Liverpool, but at the time dock workers in Liverpool were on strike so it ended up in Washington.
Similarly, when Amazon looked for a site for its first UK warehouse, it needed a location close to transport links, a relatively good supply of cheap labour and near to the point of consumption. Thus, it chose Milton Keynes, which is 45 minutes to London via the M1 motorway.
5 What is your capacity?
Does the company have the capacity to make the product? If not how can capacity be added and is this viable?
US manufacturer GT Technologies made sapphire glass, a very tough glass, which they speculated would be needed by Apple in the manufacture of its iPhones, as it was already used in high-end Swiss watches.
It invested $500 million in a new manufacturing plant, but the supply deal never came off. So the questions are: at what stage does a firm invest to build capacity? Is the financial risk affordable? And will demand go away?
There are chip shortages now, so there is a great demand for them, but it takes 12-18 months to build a chip manufacturing plant; will that demand still be around?
Either a company needs to be agile or design a product that does not need a massive degree of high end capacity to cope with this uncertainty about capacity.
By answering these five questions companies will go a long way to making their supply chain more strategic and resilient in the face of an increasingly uncertain world, where the pandemic is liable to linger on for the foreseeable future.
Mark Johnson is Professor of Operations Management and teaches on our online Service Operations Management course.
Discover our full range of Executive Education programmes here.
For more articles on the Future of Work sign up to Core Insights here.